MMC: Making Robots More Accurate than They're Supposed to Be
Article by Senior Application Engineer David McMillan. David has been in the robotics industry for more than 20 years, and is one of AMT’s go-to people for new or unusual technologies. For more information on AMT’s expertise in robotic applications, visit this link.
Move, Measure, Correct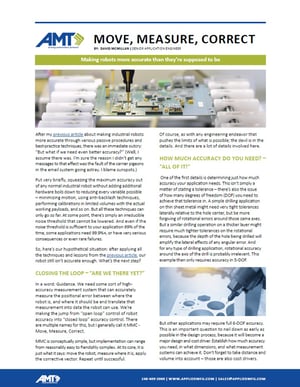
After my previous article about making industrial robots more accurate through various passive procedures and best-practice techniques, there was an immediate outcry: “But what if we need even better accuracy?” (Well, I assume there was. I’m sure the reason I didn’t get any messages to that effect was the fault of the carrier pigeons in the email system going astray. I blame sunspots.)
Put very briefly, squeezing the maximum accuracy out of any normal industrial robot without adding additional hardware boils down to reducing every variable possible – minimizing motion, using anti-backlash techniques, performing calibrations in limited volumes with the actual working payloads, and so on. But all these techniques can only go so far. At some point, there’s simply an irreducible noise threshold that cannot be lowered. And even if the noise threshold is sufficient to your application 99% of the time, some applications need 99.9%+, or have very serious consequences or even rare failures. So, here’s our hypothetical situation: after applying all the techniques and lessons from the previous article, our robot still isn’t accurate enough. What’s the next step?
Download to read the full article.
If you have questions about a specific application, please contact us.