How Integrating an AMR Can Provide Value in Manufacturing, Industrial Facilities
Originally featured in Plant Engineering’s Global System Integrator Report, AMT’s Innovation Manager Jason Markesino and Lead Automation Engineer Chris Gomez authored, “How Integrating an AMR Can Provide Value in Manufacturing, Industrial Facilities.” The article explores the growing number of applications, advantages, and design considerations for implementing autonomous mobile robots (AMRs) in industrial settings. Click here to download the full article.
Learning Objectives and AMR insights
- Understand key technology advancements with autonomous mobile robots (AMRs).
- Learn what’s needed for the integration of an AMR fleet.
- Learn how to connect the AMR fleet to the industrial control system (ICS).
Autonomous Mobile Robot (AMR) Insights
- Technology advances empower autonomous mobile robots (AMRs) to accurately map and navigate environments, boosting their adaptability and ease of deployment across dynamic industrial settings.
- Artificial intelligence (AI) and machine learning (ML) enhance AMRs by enabling real-time decision-making and efficient operations, learning optimal paths and improving object recognition through advanced machine vision.
- Battery advancements in AMRs operational hours and efficiency, ensuring consistent performance in demanding industrial environments with minimal downtime.
Experienced autonomous mobile robot (AMR) system designers can help integrate innovative and cost-efficient solutions that address many challenges in manufacturing and industrial facilities.
An autonomous mobile robot (AMR) is a type of industrial mobile robot (IMR) designed to move freely throughout a facility, completing tasks without the need for fixed pathways or regular human guidance. Equipped with several sensing technologies and onboard intelligence systems, AMRs now have the information and processing power to sense, interpret and navigate through dynamic environments. Light detection and ranging (LiDAR) systems, cameras, vision systems, pressure sensors, encoders, inertial measurement units (IMUs) and even ultrasonic and infrared sensors collect information about the current environment as well as the AMR’s motion within it. This information is then analyzed using data processing algorithms including different types of artificial intelligence to create a map of the AMR’s surroundings, allowing it to plan routes and make decisions for obstacle avoidance (see Figure 1).
Figure 1: MiR’s fleet manager software illustrates advanced navigation and fleet coordination for autonomous mobile robots.
Further expanding its capabilities, AMRs can now be outfitted with a top-mounted robot, called a mobile manipulator. AMRs come with a variety of payloads, ranging from 250 kg to more than 1350 kg. As an example, AMT has worked with manufacturers in the automotive industry to move heavy pallets of engine transmissions using larger AMRs. These include high-payload AMRs that can be coordinated for simultaneous movement of bulky and heavy parts such as an airplane fuselage in the aerospace industry. When using a mobile manipulator, the effective payload may be decreased depending on the location and orientation of the weight.
With guidance from an experienced integrator, a fleet of AMRs can be commissioned with minimal downtime in a few days' time for wide-ranging applications, including material handling, machine tending, sortation and more (see Figure 2).
Figure 2: An engineer supervises the operation of MiR’s autonomous mobile robot, designed for efficient material handling in industrial environments.
Five Key Technology Advances in AMRs
The growth of AMR use cases is driven by the maturation of key technologies. Five of the biggest are highlighted.
1. Simultaneous localization and mapping (SLAM) technology: Perhaps the most important recent advancement, the maturation of SLAM technology has increased AMR capability and ease of implementation and commissioning. SLAM technology uses a variety of sensors, including LiDAR, cameras and IMUs to gather information and create a map of the current environment.
The AMR detects fixed points such as walls and posts to accurately localize its position. This information allows SLAM to determine the AMR’s current position and motion within the environment. SLAM enables the AMR to interpret, map and navigate its surroundings.
2. Artificial intelligence (AI) and machine learning (ML): AI and ML algorithms allow the AMR to analyze the large amounts of environmental data collected by its sensors to make informed decisions regarding navigation and operations. Some types of AI now integrated into AMR technology include:
● Machine learning analyzes patterns in sensor data, allowing the AMR to learn from previous operations. For example, an AMR will learn the most efficient paths and times to perform an activity based on past experiences.
● Machine vision is used in object recognition, which allows the AMR to use visual information for navigation and task completion. Machine vision interprets data from cameras to identify paths, obstacles and previously known markers. Deep learning has become a primary approach to machine vision because of its ability to detect patterns within an image. In the context of AMRs, this technology facilitates object detection, image classification and even facial recognition (see Figure 3).
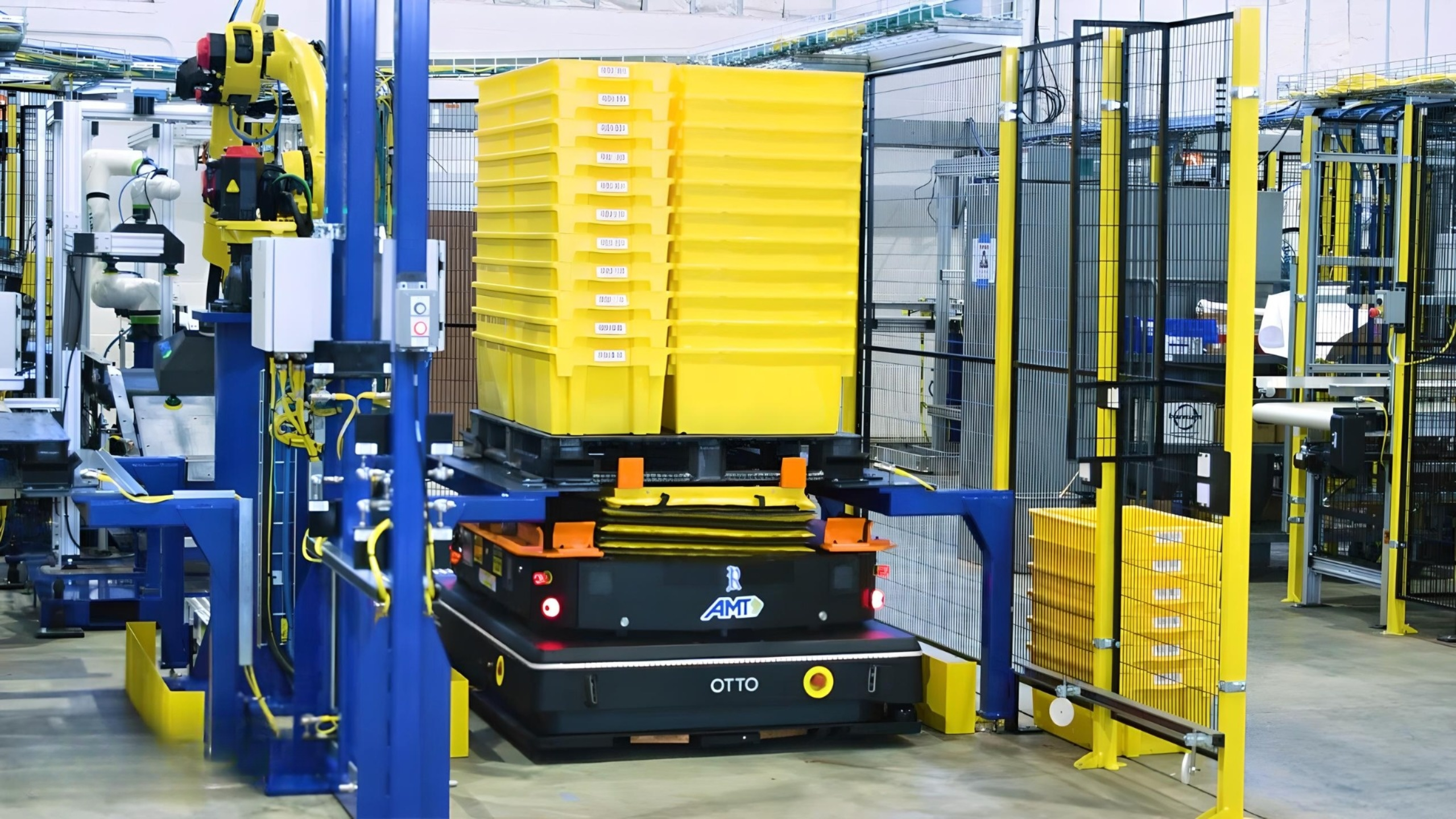
Figure 3: OTTO Motors’ autonomous mobile robot efficiently transports stacks of yellow bins, streamlining material handling processes in an industrial setting.
3. Collaborative robots (Cobots): The integration of AMRs with a cobot (known as a “mobile manipulator”), which is designed to safely operate within human proximity, expands the potential tasks an AMR can complete. For example, depending on cycle time requirements, an AMR with a top-mounted cobot can perform many tasks at different stations. This allows for greater flexibility as the automation is not fixed in place.
4. Battery technology: AMRs benefit from the energy improvements offered by Lithium-ion (Li-ion) battery technology. These benefits, including high energy density, longer lifespan, and fast charging times, enable AMRs to operate for 8 to 12 hours on a single charge, although this timeframe is application dependent. Newer AMR models with advanced battery technology can operate for 15 to 20 hours between charges. Some AMRs also support fast charging technology, further enhancing their operational efficiency.
5. Onboard computing: Improvements in processing power enable the AMR to perform the complex computations locally which are necessary for its decision making for navigation and operations. This edge computing capability reduces the latency associated with data processing compared to centralized or cloud-based computation. The result is improved robot reaction times and more effective real-time decision making.
Because of AMRs’ flexibility and ease of implementation, they can displace several traditional manufacturing and logistics systems and tasks across multiple industries.
How AMRs are a safer alternative to forklifts
Due to their extensive environmental sensors and safety features, AMRs are safer in high-traffic environments compared to traditional operator forklifts. Many industrial facilities, including manufacturing plants, warehousing and logistics centers, distribution centers and processing plants have chosen to implement a fleet of AMRs for material handling in high human traffic environments. As a result, forklifts have been redeployed to the more segregated areas of the facility for dock loading and unloading tasks.
Six Ways AMRs Can Replace Conveyors
Another interesting application gaining significant traction within industrial settings involves using AMRs to replace traditional conveyors. While conveyors remain the stronger choice for high volume, high-speed, fixed-path continuous flow applications, AMRs excel when flexibility, dynamic routing and adaptability to multiple tasks is preferred or required. The advantages of using AMRs for this purpose include:
- Less floor space: AMRs do not require dedicated floor space like conveyors.
- Non-fixed installation: AMR implementation requires minimal infrastructure change.
- Ease of scalability: When more throughput is needed, adding additional AMRs is generally easier than expanding a conveyor system. The program developed for one AMR can usually be duplicated into others.
- Adaptability and flexibility: AMRs do not require dedicated, fixed pathways. Using SLAM technology, they dynamically and autonomously adapt to layout changes. This can be particularly helpful in fulfillment centers, where product locations and volumes may change. AMRs can be reprogrammed for new routes and tasks very quickly without physical infrastructure changes.
- Potential for lower initial investment: Compared to traditional conveyors, implementing AMRs can be cost competitive. This is particularly relevant for complex paths that may be in manufacturing facilities with varying production processes requiring material transport between production cells.
- Versatility: AMRs can take on more than just basic transportation tasks; they are also capable of tending machine centers and performing picking, placing and sorting tasks.
Five Things to Consider When Integrating an AMR Fleet
Important aspects and potential limitations to consider in AMR system design include:
- AMRs take up a larger area than expected once the safety field surrounding the base unit is considered. As a result, smaller areas are inherently difficult to navigate and necessitate a targeted solution.
- When choosing the size of fleet to be implemented, consider the frequency of missions, the distance the AMRs will cover and the overall mission cycle time. The size of the fleet will also be dependent on the ability to meet the Wi-Fi network port availability, speed, and bandwidth requirements.
- A robust automated system requires well-planned error state recovery. Some common errors to consider include an AMR that is unable to get to its destination and an AMR stopped in the middle of a mission.
- Current challenges to AMR operation include environmental temperature and humidity changes that result in condensation on the optical components. Direct sunlight also can interfere with their safety scanners. The floor surface is also critical: Concrete works well, carpet is less suitable and wet floors can cause slippage, which can interfere with the wheel rotation counts used to track displacement, leading to positioning errors.
- When implementing an AMR fleet, additional program design is needed to ensure they don’t trap themselves in an area. One way to handle this error state is by setting up traffic zones, allowing only one AMR into a given zone at a time.
AMRs Require Expertise for Full Integration
Another challenge to AMR implementation involves their integration with other automation control systems, including programmable logic controllers (PLCs). Most PLCs cannot directly initiate missions for AMRs, which means an intermediary system is required to facilitate communication between them.
Fleet manager software coordinates the operations of multiple AMRs within a facility (see Figure 4). Using an application programming interface (API) calls for communication between the AMR fleet manager software and associated AMRs, as well as for incoming requests to the fleet manager from other control systems. However, due to their focus on real-time industrial communication, most PLC brands are not able to generate web-based communication such as an API call.
Figure 4: Engineers collaborate using OTTO Motors’ autonomous mobile robot in a warehouse setting, highlighting the integration of advanced robotics into industrial workflows.
One way to solve this problem is using a middleware software platform that connects to the PLCs via industrial protocols and Python scripts that generate the associated API calls to communicate with the AMR fleet manager.
Using an example case of a PLC requesting more parts, the AMR system operates as follows:
● The PLC monitors production processes. When it detects a need for more parts, it communicates with the software using standard protocols (i.e. OPC UA)
● The software detects the tag change and using a python script translates the request for more parts into an API call.
● The API call is sent to the fleet manager and may include details about the type and quantity of parts needed and the timeline.
● The fleet manager selects the best AMR to deploy for the task. For each AMR, it may consider its current workload status, relative proximity to the target work environment, and even current battery status.
● The fleet manager generates an API call to communicate with the target AMR to dispatch it for the task. The call will include details of the operation, including location of pickup and drop-off.
● The AMR obtains the additional parts and delivers them to the requesting PLC’s production line at the drop-off location.
The value of working with an experienced integrator for AMR implementation cannot be overstated. An experienced integrator understands PLC and AMR communications and knows how to use middleware software as an intermediary, allowing them to effectively integrate an AMR system with existing automation technology.
The growth of AMRs for solving common manufacturing challenges has been driven by key advances in sensing technologies and data processing capabilities. These advances have increased the breadth and complexity of tasks AMRs can now complete while simplifying their implementation. Working with an experienced integrator, an AMR solution can be designed and implemented quickly with minimal on-site downtime. Experienced integrators can help manufacturers address remaining AMR integration challenges, positioning them for rapid adoption of this flexible and scalable solution.
Click below to download the full article.