Craig Salvalaggio Explains How Integration Advances Competitiveness
On March 8, 2023, AMT President Craig Salvalaggio participated in a CFE Media webcast “How Control System Integration Advances Competitiveness,” where he discussed future applications that will allow businesses to stay competitive and push the boundaries of automation and technology, with examples on robotic applications related to warehousing.
Read the original article “How control-system integration advances competitiveness” at Control Engineering.
Article by AMT President Craig Salvalaggio
Automation in warehousing is a growing trend which involves complex material handling, equipment sensor technology, conveyance, and data tracking software to solve unique challenges at very high speed. Labor shortages continue to impact the growing warehousing and e-commerce markets. We must look to identify what best in class technologies are out there to solve the complexity in the warehouse.
Who Doesn’t Want to Enjoy Their Job?
As we examine automation: the features, and benefits and the ‘why,’ we ask, who doesn't want to enjoy their job? With automation, we seek to reduce manual labor required and the cost associated with it, upskill those individuals and repurpose them for more fulfilling roles. You talk about the cost of training by creating a fulfilled life.
You're lowering cycle times by increasing throughput, line speed and overall system efficiency. You look at the cost per touch, so, cost per pick: what does that do when you're growing and increasing your throughput and you're scaling? You look at the repetition that's happening when you're picking and placing boxes in a warehouse and the heavy loads associated with repetitive tasks, and then you're integrating in cutting edge technology and software to be able to address these key edge cases.
Warehousing Automation Application Terminology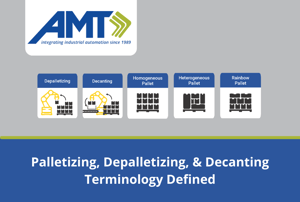
When discussing warehousing automation applications, there are a few terms you need to know. When materials are fed into a storage system or they’re being processed, typically depalletizing is involved. There are multiple types of pallets and how product can be loaded into them. To learn more, be sure to read our palletizing, depalletizing, and decanting terminology definitions.
Case Orientation: 2D Versus 3D Vision Data
You can stage the material so you're having fewer touch points utilizing the power of a complex 2D or 3D vision system, which allows you to look at the product upstream and position it or rotate it before grasping it. There are tricks such as pre-staging the product to one side as it comes in, especially when you're dealing with a quick 1.5-2 second per pick cycle time. Then, you look at drag coefficients as far as rotating or positioning the boxes and really what that means for the system.
From that perspective on the backside, you need to pull the boxes out of the storage system. We refer to this as de-traying or single/multi picking. This is really a different set of challenges because the boxes that get stored in the layer can then be jostled or moved during the conveyance portion of it, and you must pick those with a single multi-zone end-of-arm tool (EOAT).
Utilize 3D vision systems to find all the boxes and return their positions. Writing the algorithms through those group picks allows you to pick optimally on the tool. We combined 3D-vision data with 2D-vision data to protect the image detection and image processing for throughput. And then, understanding from a design perspective, how do you lay this all out to get optimal cycle time and throughput?
Related: De-tray and layer forming robotic system for Gojo Industries
Planning for Control System Design, Implementation, and Simulation
Preparation, planning, and communication seem basic, but it goes back to the premise for a lot of foundational items. Learning how to plan for control system design, implementation, and simulation: what are the tools and how do you approach it? Before you design anything and before the teams get together, what do you look at from both a pallet perspective, a product or SKU perspective, and then technology?
If you're looking at the pallet, there is a lot of variability that happens within warehousing applications, and so you want to ask yourself these fundamental questions:
- How much information do you know about the pallet?
- Slip sheets, orientation, label placement, etc.
- What data do you have?
- Do you have the pattern?
- Do you have the layer?
- Do you have the weight?
- How is this data stored in your warehouse management system (WMS)?
- How is it translated down to the technology-level algorithms?
Acknowledge the possibility of patterns that can be mathematically calculated with a few data points, row columns, rotations, or grid-based patterns. When using a slip sheet, understand the material, the texture, the ability to find them, the load stability, or we call it a ‘load triangle,’ if eventually moved with an Autonomous Material Handling (AMR) system. When the pallet moves, how stable is the product based on where the contents are in your patterns?
There is complexity in what's required to stack a box in a predetermined pattern, or in your predetermined layers. Can the system handle partial pallets? There is a lot that goes into it: the number and degree of complexity of the patterns, your product variability, product integrity as far as case dimensions, and then the volume of SKUs in these kinds of applications. You may have to design a system where you get, for example, 10% of the product and it may be some of the edge cases and the system may see 5,000 SKUs over its time, but you won't see those until after integration. So, you must ask yourself these types of questions well ahead of the design phase. It goes back to these questions: How do you plan, how do you design, and how do you simulate the needs of what might be involved in these types of applications?
Product Range – What is Your System Looking At?
A system with a large product range can accommodate the large range of box sizes, dimensions, surface tops and deformation. Box dimension ratios can be important too. You have tall, skinny boxes that are tippy versus short, wide boxes that may have a bow in the seal. When you're using vacuum technology, you want to look at the porosity of the box material that comes into play. You want to look at the materials and how that could potentially shed into the vacuum lines and interfere with maintenance. You may need to use a combination of vacuum and clamping depending on the forces and speeds at which you're operating. From a product standpoint, you're looking at the product itself, the range, the features, and the printing.
AMT really grew up in automotive where we were used to handling large, heavy metal parts that hold contour and shape. But as you get into warehousing applications, there are many teams that create highly graphical packaging, which is more desired by the consumer. As that all translates into sales, it's very difficult for the automation to be able to handle that many different use cases. You're looking at highly graphical boxes, boxes with openings, boxes with reflective tape, slip sheets, case integrity – all these types of things that impact how a vision system or a picking tool would handle the automation.
EOAT Technology
There is a variety of technology to sort out on these systems. You're going to break this down into dipping, grasping devices. This could be vacuum cups or vacuum pads. Those pads could have different zones on them to accommodate a single pick or multi-pick application depending on the surface that you're after.
There are many ways to handle these problems. With the vision systems, you have lighting challenges impacting the ability to take images of these different graphical boxes and be deterministic about finding the results every time.
You also have 3D complexity: human vision versus machine vision. In these types of applications, you have so much SKU variability and volume that being able to plan, store the data, and transmit the data down to the system means you really want to do that planning, learning, and simulation well ahead of time.
You get down to the per-SKU level and you're looking at just the variability, case integrity, the printed and graphical matter, the patterns, and the material that holds the pallet together (whether that's corner boards or slip sheets). It’s important to have the ability to do this in a non-machine-learning environment so your system doesn't need to have the product to be able to gain its integrity as far as the reliability of the application.
Lessons Learned in Automation Implementations
How do you continue “to sharpen the saw,” as Stephen Covey would say? How do you continue to improve and continue to make our teams better? We will be discussing business objectives, but at the end of the day, it doesn't matter what you're looking at. Whether it be an automotive part, an aerospace part, flexible or rigid plastics; it could be a warehousing application. Part of your takeaway here is to study the product, how it behaves, how it's defined, and what the measurables are.
Questions to ask are as follows:
- How will you measure success from a metrics perspective?
- Does it come down to perfect cycle time?
- Does it come down to system fill and system throughput or are there other objectives?
Use the available simulation tools. There are PLC simulation tools, discrete event simulation tools, robot kinematic tools that can give you your theoretical versus actual. One of the biggest outcomes is collaborating with your customer, making it one team, one approach and learning and working together with one another. You break that down as you're designing the system and how you look at the differences between business versus technical objectives as you are in this planning phase and considering the bigger picture. If you're part of an automation stakeholder team, you're starting to look at the longer-term view. We look at these more as system attributes versus automation objectives. There are some things to consider as you go through this with your customer, whether it's a ventilation system or warehousing application, whatever it may be.
Ask yourself:
- Is it scalable?
- Can I duplicate the automation?
- Is it flexible?
- Can I run the current product versus next year's product?
- Can it be redeployed?
- Are my facilities laid out?
You may have future plans to introduce AMR technology to deliver products to and from the automated cells. If you do, you want to look at the size of your aisles, the pitch on the floor, and transitions between different foundations. There is more. You want to look at your manufacturing risk and look at your risk tolerance and degrade or backup plans versus manual or human interaction technology. You want to look at where things are from a technology maturity standpoint. Is this bleeding-edge technology that doesn't have a lot of use cases or is this something that's running in factories every day? You want to look at your material design, your material flow, scheduling, and reoccurring downtime, and then quality and system byproduct. You may have a reclaimed system depending on the byproduct.
You need to take information and overlay the usable technology. There could be different types of traditional robotics versus power-and-force-limiting types. Some people may understand the term ‘cobot,’ or power-and-force-limiting robot, where, depending on the application, it could be introduced without work cell perimeter guarding. The simulation tools allow you to plan and test scenarios and potentially conduct virtual commissioning. There are technologies that use additive manufacturing to do earlier “fail fast” on R&D. You can also use horizontal versus vertical integration, meaning you can prepare your team internally to be the stakeholders, or you can use outside integrators at a variety of different levels. Be aware that cybersecurity influences data collection, and that data can make your system work more intelligently, from machine learning and predictive maintenance to predicting downtime or premature failures.
You want to focus on worker augmentation, not replacement. You're upskilling and really value adding jobs. You want transparency in the data, ensuring that your people know what's being measured and how it impacts them directly so they can really drive the decisions they're making. You want to improve decisions through analytics by making smarter decisions with the data. And then, you leverage those technology platforms and use partners or your in-house capabilities to set yourself up for success.
In closing, decide what business you're in, what your core competencies are, and leverage the ecosystem that's in the Control System Integrators Association (CSIA) and other industry associations to collaborate, share information and learn from one another so that everybody gets better.
Audience Questions Answered
How Valuable are Simulations?
I look at simulation in three degrees of difficulty. One, it could be used as a planning tool for visualization conceptualization on potential system designs: how that looks in your factory and looking at scenario planning better than with just a 2D layout of the process. I think the simulation tool, from that perspective, adds a lot of value. Take that a step further and then simulate your speeds, your throughputs, your payloads, your kinematics, etc. I would call it a ‘throughput simulation’ or ‘discrete event simulation’ versus ‘cell simulation.’ With these tools, you can start doing more engineering-level work and provide feedback for offline programming and reduced integration and onsite installation time. The third aspect of simulation is probably the most difficult, it is truly creating the digital twin.
To make a digital twin successful, you first use the tool, then use it to create the program. Finally, you document anything that changes within the work cell, which is as-built drawings or what happens in the facility. You upload that back to the digital model to be able to keep that model up to date, which is probably the most disciplined aspect of using the tool. If you have the processes and you have the capabilities and the software tools, a digital twin provides a ton of value. Probably the most difficult task is ensuring that live data from the plant floor is fed back into the model to be able to use it correctly.
When Should Digital Twins Be Used?
If you look at the cost of software, the cost to implement, it makes sense to use a digital twin when larger organizations get critical mass with deploying technology. If you look to the near future, I think you're going to see digital twins being adopted. I think you're going to see software costs coming down, use cases implemented, and the value starting to be provided. I think it's going to take some larger companies to drive that through the system to be able to get critical mass in the industry.
Control Programming Tips
I think everybody probably understands that new people are entering the industry right out of college or from another profession, and there are varying degrees of ability to use PLCs from what they've programmed in their pasts. A lot of times, it goes back to those foundational principles. And, it's easier said than done, but plan and prepare, then break the system down to a sequence of operations. I always go back to the question: Does the company or team have a standard set of libraries? There's a section of conveyor: do they have a library that they can pull up if they're controlling a robot or a vision system? Can that be a standard module? Having that standardization can lead to success.
Can Automation Safely and Effectively Integrate with Cloud Infrastructure for Smart Manufacturing?
I've been on this journey for about five years now and a lot of things are changing. The technology platforms are changing as far as what can be done and how the data can be stored. A lot of it goes back to educating the end user, making them feel comfortable with the technology, and then showing them what value it can provide back to their manufacturing operations. Is it doing some predictive work? Is it allowing you to have more intelligence about your machines and conduct repairs more quickly? Is that value case laid out ahead of time? I still think that in the five-year view, it's not going away. We're going to get smarter. The technology platforms are likely going to change multiple times, but someone will continue to take the lead and continue demonstrating use cases that are valuable to an end user who must maintain the equipment.
If you want to learn more about the details discussed in this webcast, you can tune in here.
To discuss your project, please reach out.