Michael Jacobs Shares Overview of Robot Industry to CEOs
Applied Manufacturing Technologies’ Founder Michael Jacobs presented ‘The State of System Integrators and Robots’ to Chief Executives Organization.
As defined by Wikipedia, robotics is an interdisciplinary field that integrates computer science and engineering to create machines that assist humans. Today’s robotics industry can be broken down into several major categories, based on where the products are in their stage of development, from mere ideas to equipment in full production.
Robots in the concept stage are still being developed and tested to determine the market’s interest. With alpha testing, devices are still in the labs and being tested to ensure it meets the business need and functions correctly. When a robotic device enters beta testing, it is made available to a group of users to evaluate the product in a production environment.
After the product’s initial release, it is further evaluated by early adopters in a limited market penetration. Once it has successfully navigated the early adoption phase, the robotic device may be widely accepted into the production environment. An “everyday” robot application has reached widespread, perhaps ubiquitous adoption.
Robot Concepts
The word “robot” was coined by Czech playwright Karel Capek in his 1920 science fiction play Rossum’s Universal Robots. People have been dreaming of what these devices might do ever since. From Star Wars’ R2D2 and C-3PO to Isaac Asimov’s 1950’s I, Robot, we still haven’t achieved all the capabilities of these characters.
Corridor Digital’s more recent cinematic gun-toting robots caused quite a stir causing people to ask if walking robots can carry guns. Those of us that work with robots know it can’t be real; not today. Will they be capable of that someday? Yes, I think they will be.
Robots in Alpha Testing
The robots in alpha testing are real; they are in labs but not yet installed in the field. Boston Dynamics has a video of one four-legged and two humanoid robots dancing. The ability to balance and move like that on two legs is truly amazing. The production quality of this video is high, but it’s definitely a lab environment. If you don’t believe me, search for the blooper clips, which show what it took to get that final video.
Kawada Robotics from Japan has several models of collaborative humanoid robots, including HRP, Humanoid Robot Platform for research. Kawada also has Nextage for industrial applications which is in the early adoption phase.
AMT has partnered with Soft Robotics, a company that provides cutting-edge robotic systems with soft robotic grippers and 3D vision solutions. Soft Robotics has a set of configurable grippers that can safely pick up objects such as food items that are hard or soft, sturdy or fragile, light or heavy, allowing food industry clients to automate their processes.
Robots in Beta Testing
Beta tests are pilot projects: robots that are fresh out of the lab, put into real production to see how they react. AMT is working with several industry leaders who are currently in beta testing for their products.
Plus One Robotics is a company that is attempting to solve some complex projects in the logistics space. As occurs in order fulfillment, picking random objects from a disorderly bin is a tough problem. The system’s vision, AI, and robot can’t always find a solution, and when the system gets stuck, a remote operator is notified to direct the robot how to pick.
AMT is working with Innovision, a company that has a system that can find defects in freshly-painted surfaces. In this video, freshly painted auto panels are moved through the Smart Inspect tunnel where a vision and AI system finds the defects and classifies them. The quality inspector can interact with the system through a touch panel. Afterwards, the defect type and its location are communicated to a group of robots downstream that are then able to automatically repair the defects.
AMT has also partnered with Liberty Reach, whose VPick decanting system, together with an AMT robotic cell, will soon be in beta testing. The problem is to de-stack a pallet of boxes and to do so such that the robot picks an optimal number of boxes to fit into a warehouse storage tote. There can be over 3,000 different box types and they need to be handled, even though they haven’t ever been seen by the system before. The system uses vision, AI, and robotics to achieve this.
In industry language, the system performs optimized multi or singular pick-and-place operations from uniform pallets into a defined space or container. Using industrial, full-geometry 3D vision, the system accurately picks from both mixed pallets and pack containers. The VPick decanting systems function without knowing the number of boxes on a pallet layer. The system accommodates a large range of box sizes with a variety of printing, colors and finishes. The box sizes can either be known or random and the system can perform a single-box pick or a multi-box pick in order to optimize volume. VPick decanting software does not require the boxes to be stacked according to any predetermined pattern.
Early Adoption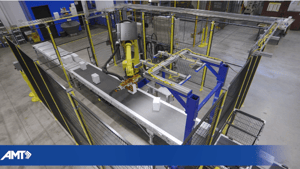
Moving beyond beta testing are systems that have been deployed in a full production setting by early adopters of these new technologies.
This AMT system was recently installed in a warehouse, and its job is to play “Tetris” with the boxes on a moving conveyor belt. The boxes are being moved into their appropriate spots in rows and the rows will form a layer to be placed on a pallet. Like Lucille Ball in the candy factory, the belt never stops and the product keeps coming. The system uses 3D vision and line tracking to guide the robot to re-orient the boxes.
Another AMT system was recently installed in multiple plastic injection molding facilities around the US. It uses a FANUC CRX, a new collaborative robot. This system picks freshly made totes, places labels and RFID tags on each side, inspects the quality of those labels, rejects the bad ones and stacks the good ones. Also of note, AMT manufactured parts of the robot gripper with 3D printing.
Here’s a photo of me taken in our shop. I’m 6’2”, or about 1.9 meters tall. I’m standing beside a FANUC M900 robot, one of the largest standard product industrial robots made, capable of lifting 700 kg, over 1,500 lbs., and placing it within fractions of a millimeter all day, every day, without fail. The robot itself weighs 2800 kg, over 3 tons! It will travel up and down this rail to store and retrieve these coils making this a robotic ASRS.
Here’s a simulated image of what that system will do.
Robot simulation is a computer graphics tool that system designers use to gain assurance that the entire system will do the job as intended before any metal or equipment is committed to.
This system is for an aerospace manufacturer. Rolls of various material are stored by the system and retrieved when the Factory Management Software calls for their use by other machines. This simulation shows all identical rolls of material for convenience. The real system will store coils of various materials and differing sizes.
Everyday Robotic Applications
Everyday robotic applications have been used in industry for 20-40 years, but that’s not to say these are low tech. As the technology improves, so does the capability and performance of these applications.
Recall why we deploy robots at all: replacing or augmenting human jobs that are the “three Ds.”
Dirty, Dangerous, or Demeaning
Here’s a job that’s all three! This plant recycles aluminum, and those freshly-made ingots are about 600 degrees Fahrenheit. This current AMT system is in the final design and parts are on order.
Here’s a simulation of how the AMT system will solve this problem:
The next example is from an AMT customer that packages meat. The system we designed and built is comprised of conveyors, x-ray inspection machines, scales, and robots. These all work together to inspect product safety, and get the right amount or weight of burgers on the right pallets. A meat processing plant is kept at about 45 degrees Fahrenheit year-round, the same temperature as your refrigerator…Not a pleasant place to work all day.
This system saves the customer, Wolverine Packing Co., from over-delivering product by using integrated weight controls, and has saved the customer a lot of money. The system automatically moves full pallets out and empty pallets in, and automatically provides and places slip sheets, giving stability to a pallet of boxes. The full pallets are automatically stretch-wrapped with plastic film. To download a case study on this project, click here.
The Spartanburg, South Carolina BMW plant has an automotive spot-welding system for what is known as a framing station, as can be seen in this video. While this function has been done robotically for 30 years, I’ve never seen one so clean and elegant. Today, it’s not unusual to see more than 200 robots in an automotive body assembly shop.
Further down the car production line, you can see an automated and robot-driven painting process, as shown in this video. Practically every mass-produced car in the world is painted today using robots, and notice that the production line does not stop moving. The environment inside this paint booth is explosive so all the equipment is intrinsically safe. In the 1970s this job was done by people – in bunny suits – with respirators… if they were lucky.
Robotics in Today’s Manufacturing Environments
Robots do not stand alone; they are part of a much larger infrastructure of connected devices and custom-programmed software, which includes hardware and smart devices, OT (operations technology), Cloud/Edge infrastructure, and HMIs (human-machine interfaces). Below is an illustration of the details.
The Value of a System Integrator
As you can see from the above graphic, there is much complexity in today’s manufacturing systems, and each smart device may be made by dozens of different vendors. Also, no one vendor offers a complete family of smart devices, and vendors are not in the business of interfacing their products to the products of other vendors; they have a built-in agenda to use their only own products. This presents quite a challenge for manufacturers looking to gain improvements in efficiency and productivity with the myriad options currently available.
Enter the qualified system integrator (SI). The function of an SI is similar to that of a general contractor / builder. The SI’s experience when building the system ensures all the hardware and software works together to meet the end user’s needs.
End users may believe they have the capability to self-integrate robotics because they have an in-house engineering department. The staff engineers are experts in manufacturing or processing their products, but may not be experts in automating those processes. Automation is a critical process for the end user, but it is non-core.
The system integrator’s functions are to:
- Understand the end user’s goals
- Collaborate to design a custom and reliable automated system using best-in-class components from various vendors
- Build, test and run off that system
- Deliver, install, and start up the system
- Provide ongoing support, training and service
AMT is a system integrator of industrial automation with internal engineering teams that tie together all of the critical components from different vendors into a single predictable and reliable system. We integrate that system into the end user’s existing OT and IT infrastructures and continue to support the system as needed.
For more information on how AMT can help your company meet its production goals in this difficult environment of labor shortages, please contact us.